What Makes Resin 3D Printers Print Faster?
- 3D Evaluate
- Nov 23, 2020
- 2 min read
Updated: Nov 23, 2020

It might be the oldest additive manufacturing method but has no substitute when detailed, smooth surface, superb dimensional accuracy and transparent parts are required. It is the Stereolithography, mostly known as SLA.
The process main principle is well known but in short, SLA is a vat polymerization method, where layers of the liquid precursor in a vat are sequentially exposed to ultraviolet (UV) light and thereby selectively solidified.
SLA comprises many technologies that are also referred as “Resin 3d printing”. While laser scanning is the most common, technologies like DLP (Digital Light Processing), 2PP (2 Photon Polymerization), CLIP (Continuous Liquid Interface Production) and others were developed to enable higher resolution and faster production rates.
Where to start from? top or bottom?
As always with technology, one size doesn’t fit all. The products requirements will determine which machine should be used and fortunately there are more than one we can choose from.
Desktop printers might differ from industrial ones in size, layer thickness, incident light direction, optics, build rate and more. One major difference between various machines is the incident light direction or build direction.
In that aspect, there are two approaches while building a part in SLA. The first is the free surface approach (Top-down) and the second is the constrained surface approach (bottom-up) as described in the image below.

Pro’s
- Smoother surface due to more precise movement in the Z direction
- No need for a mechanical sweeper (blade) - saves time; faster production
- Less resin waste as the part is not fully submerged in resin like the free surface approach.
The main challenge of this approach is the attractive forces of the cured resin to the bottom surface which needs to be released at each layer. Two innovative and commercially available solutions are the self-lubricating membrane which inhibits the attraction of the printed part onto the bottom surface, while the other solution is the CLIP. The CLIP by Carbon uses an oxygen permeable window. Oxygen molecules inhibits the resin curing, therefore, a constant thin layer of non-cured resin (“dead zone”) enables continuous printing.

And of course don't forget, if you want a strong and healthy SLA part, do not forget to fully cure it.
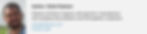